Project Story.02
3Dプリンタ用原料の開発
3Dプリンタ用炭化ケイ素原料と、それを用いた造形品の製造技術を開発しています。3Dプリンタに用いられる原料は、一般的にはプラスチックや樹脂、金属などが主流で、炭化ケイ素を原料として用いることは、これまでに事例の少ない、新しい取組みとなります。
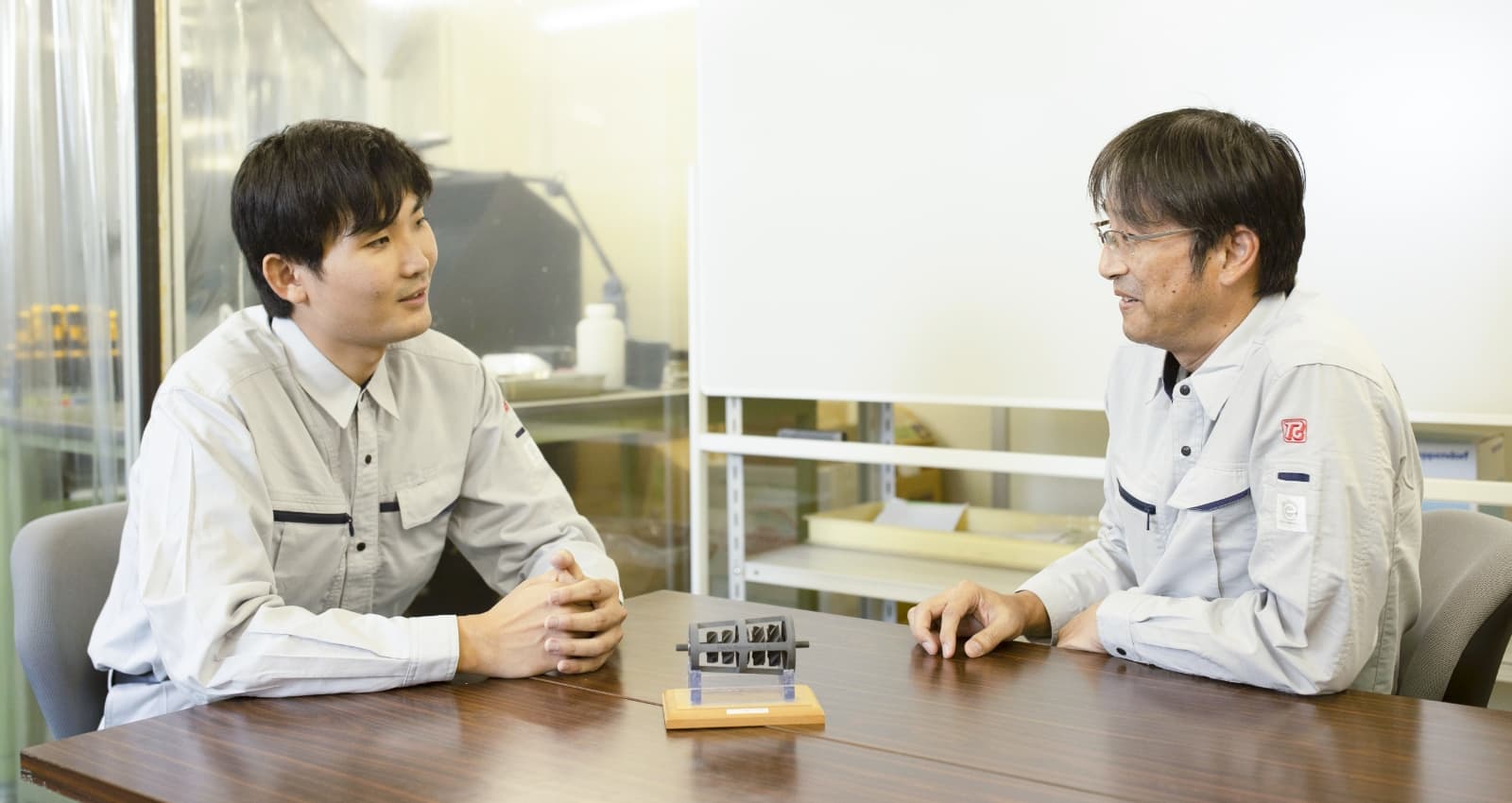
プロジェクトメンバー
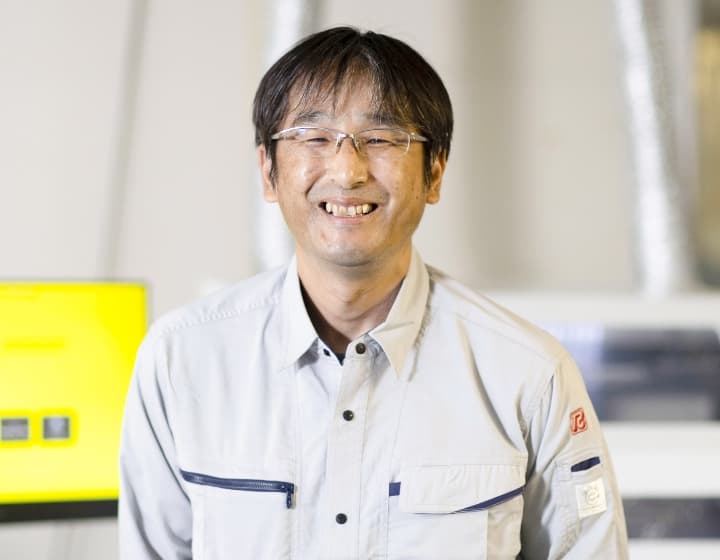
開発課長 S.K
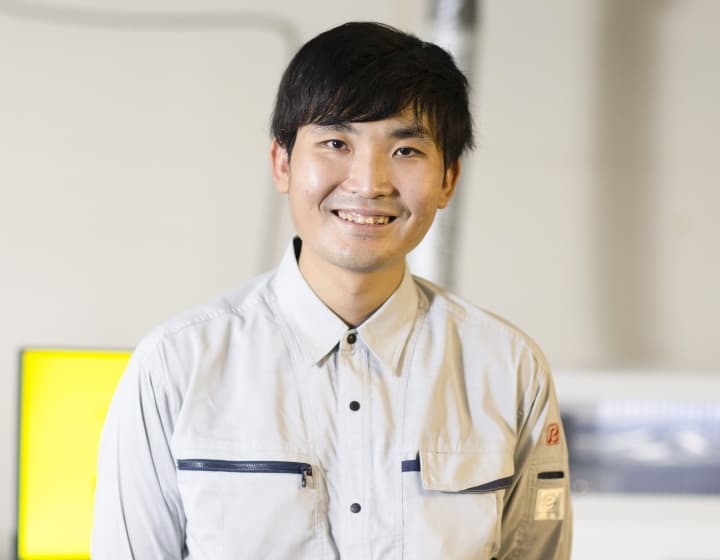
設計技術課 K.S
プロジェクトの背景と経緯
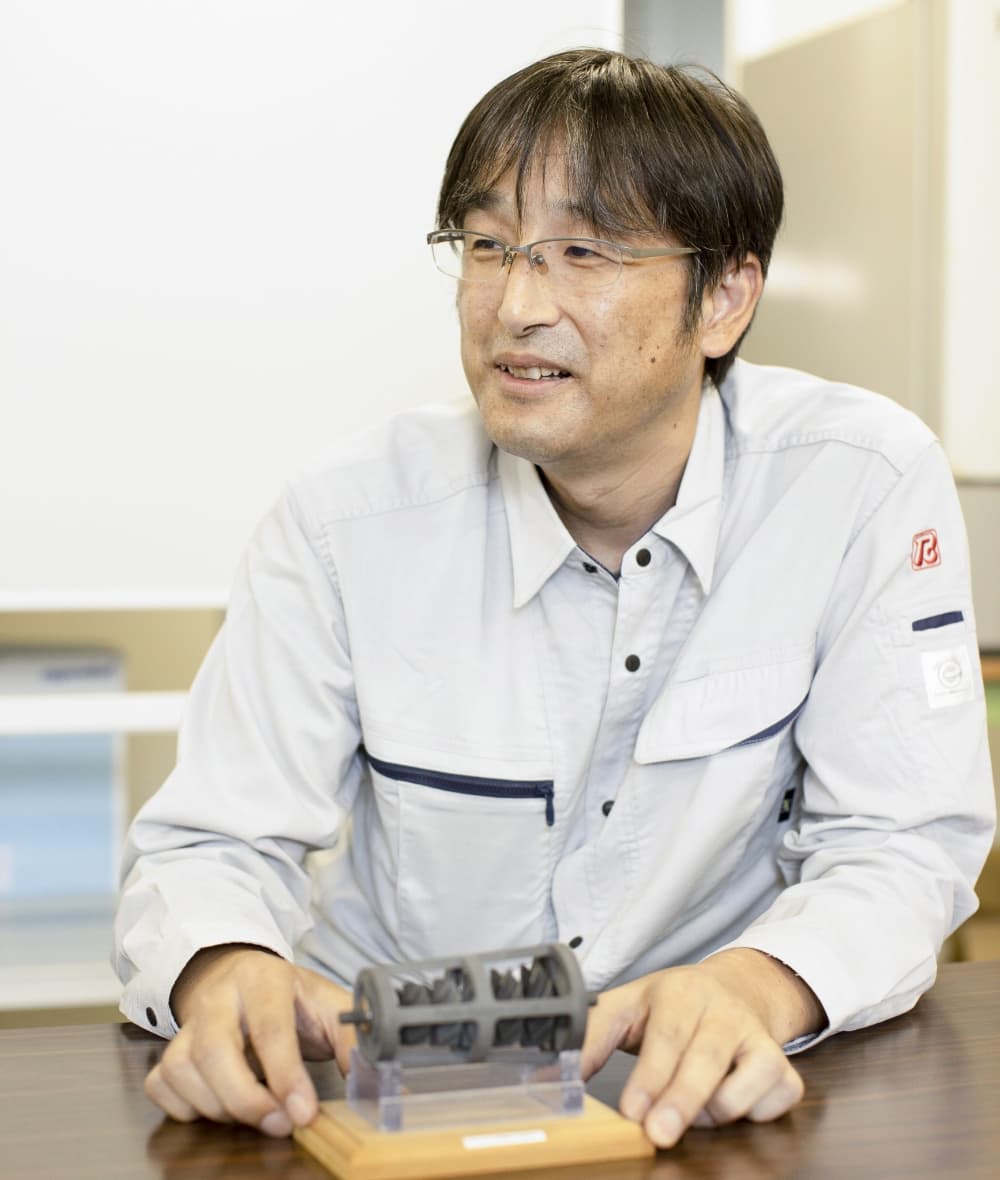
- S.K
- 炭化ケイ素メーカーとして、「当社の製品を3Dプリンタ用原料に使うことができないか?」という発想から始まったこのプロジェクトも、もう少しで10年が経ちますね。最初は、炭化ケイ素に適した3Dプリンタの出力方式の調査から始めたんですよね。
- K.S
- その頃僕はまだ入社していませんでしたが、当時は3Dプリンタ用の炭化ケイ素原料の開発事例がなく、文献なども全くなかったんですよね。知識も知見もゼロからのスタートで、初めの頃は苦労されたのではないでしょうか。
- S.K
- 3Dプリンタの原料には、一般的に樹脂や金属が使われます。それに比べて炭化ケイ素は耐熱性が高く、高熱伝導率、高強度というメリットがありますが、もろいという弱点があります。3Dプリンタの造形品で強度を出すことが難しく、これを克服するのは至難の業でした。バインダージェット方式(バインダーという結合材を粉に噴射し固めて、積層しながら造形物を作る方式)に適した炭化ケイ素の粒度配合を見つけるのは大変でしたが、さまざまな粉体を何度も組み合わせて研究を重ねました。多様な粉体を社内で製造できる粉体原料メーカーだからこそできたことです。
プロジェクトを進めるなかで、大変だったこと
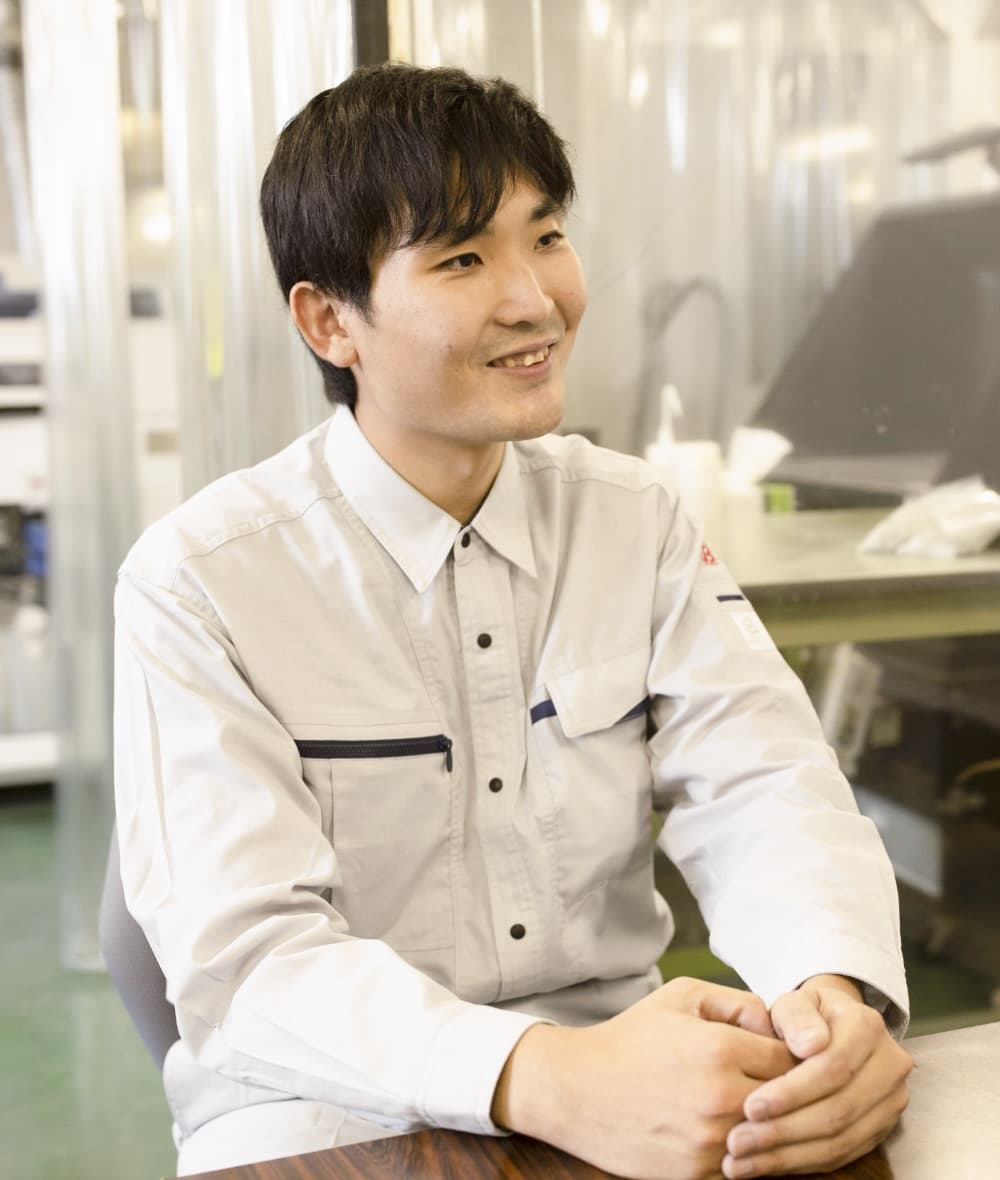
- S.K
- 開発当初の試作品は、触るとすぐ崩れてしまって、うまく造形できませんでした。原料のブレンドなどを変えて何十種類もの原料サンプルを作りましたよね。
- K.S
- はい。焼成してバインダーがなくなると、強度が低下してしまって…。試行錯誤を重ね、今では、焼成後も造形を保つことができるようになりましたね。
- S.K
- 開発当初は3Dプリンタ設備を導入できなくて、試験造形を3Dプリンタのメーカーに委託していたんですよね。メーカーのスケジュールの都合もあり、1、2ヶ月に1回程度しか試験ができず、もどかしかったですね。直接遠方のメーカーに赴いて、造形の立ち会いと打ち合わせをして造形条件や問題点の抽出をしていましたが、やってみたいことをスムーズに実行できなかったのはなかなか辛かったですよ。
- K.S
- やはり造形品の強度を高めることに一番苦労しましたよね。造形品がメーカーから輸送される間に破損していたこともありましたし…。造形に用いる設備・原料について、さまざまな条件で求める強度に達するまで、造形試験を何度も繰り返しましたよね。
- S.K
- 社内に3Dプリンタ設備を導入してから、日々造形が可能になって、開発スピードが格段に上がりましたよね。今まで困難だった形状にも挑戦できるようになり、本当に良かったです。自分たちで3Dプリンタを動かしながら得られることは大きいですね。
プロジェクトにおける喜びと学び
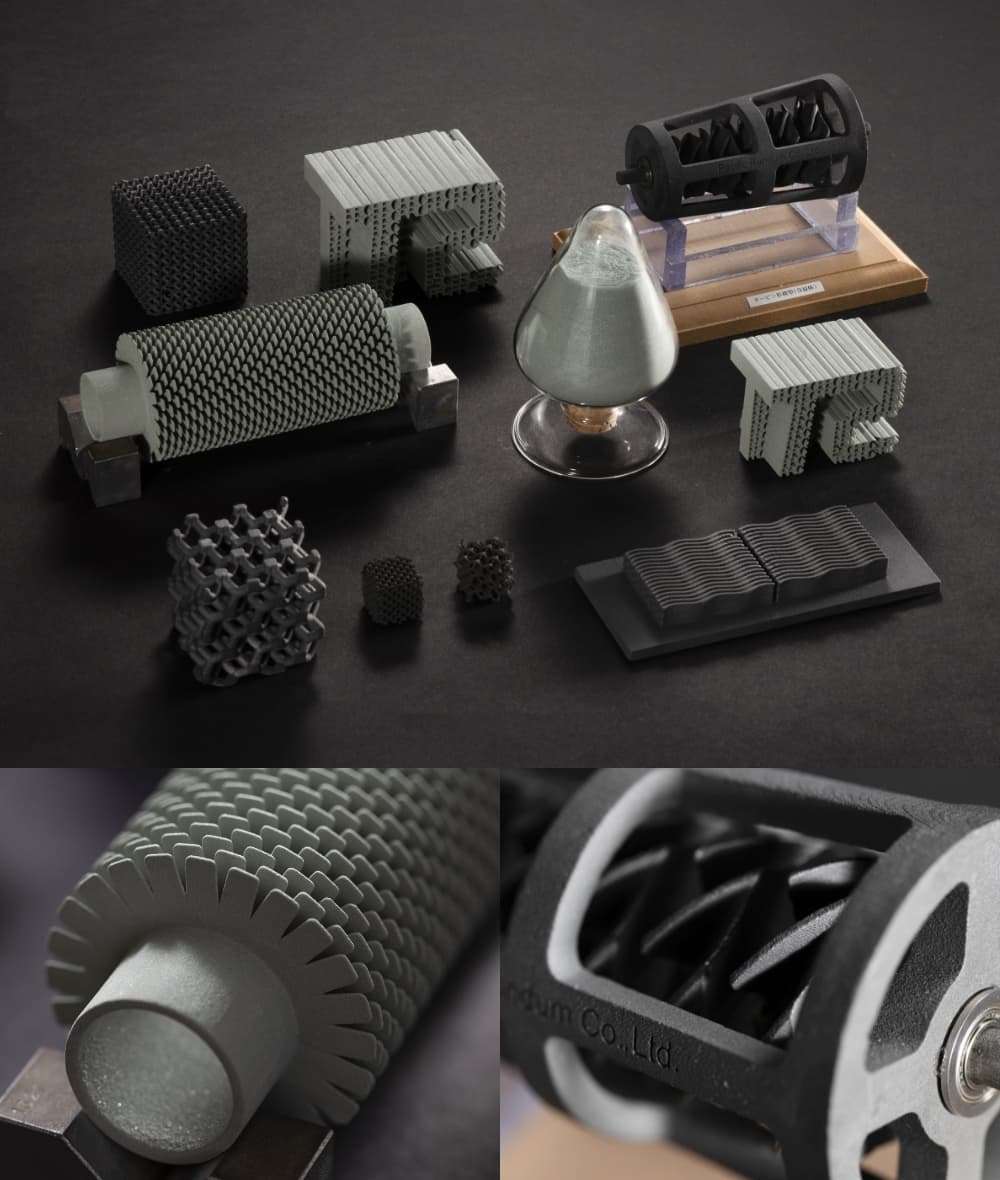
- S.K
- 強度を上げるための対策がなかなか良い結果に結びつかなくて、プロジェクトメンバーと案を出し合いながら試作を進めました。試行錯誤の末に良いデータが得られた時や、その原料を使って、複雑な形状でも精度の高い造形体を作ることができた時は、何ものにも代えがたい喜びがありますね。
- K.S
- そうですね。3Dプリンタで造形物を初めて発掘する作業で、複雑な造形物が無事に粉の中から現れてきた瞬間、言葉にならない嬉しさがこみ上げました。3D CADや3Dプリンタ機器の技術を用いることで、オリジナルかつ複雑な形状の造形品を作ることができるということに、今も感動します。
- S.K
- 2019年からは高機能セラミックス展に出品できるようになって、これも大きな進歩だったと思います。当社はB to B(企業間取引)が主でしたが、この展示会を通じてB to Cの可能性も見えてきたことは、大きな収穫でした。
初回はデザインを重視した造形物を出品していましたが、翌年から、より実用性の高いもの、工業的なものにシフトして出品したら、多くのお客様が興味を示してくれました。タービンモデル(羽根車を回転させることができる)が好評で「どうやって作ったんですか?」という質問が多かったですよ。3Dプリンタ以外のもので作るのは難しい形ですからね。
- K.S
- K課長の設計技術があってこそできた造形だと思います。プラモデルを趣味にされているということも、このプロジェクトに活きているんでしょうか?
- S.K
- どうでしょうね(笑)。造形モデルのアイデアの創造にはまだまだ課題があります。3D CADの技術についてはSくんにも期待していますよ。Sくんをはじめ、粉体の知識が豊富なメンバー、細かく粘り強く検証をするメンバーなど、いろんなメンバーが集まっているからこのプロジェクトは成立していると思っています。開発した原料はまだまだ改善の余地がありますし、3Dプリンタを大きくしたらまた違う問題が出てくるかもしれません。考えて行き詰まった時には、これまでのように「とりあえずなんでもやってみる」という精神で進めていけば、もっといいものができそうですね。
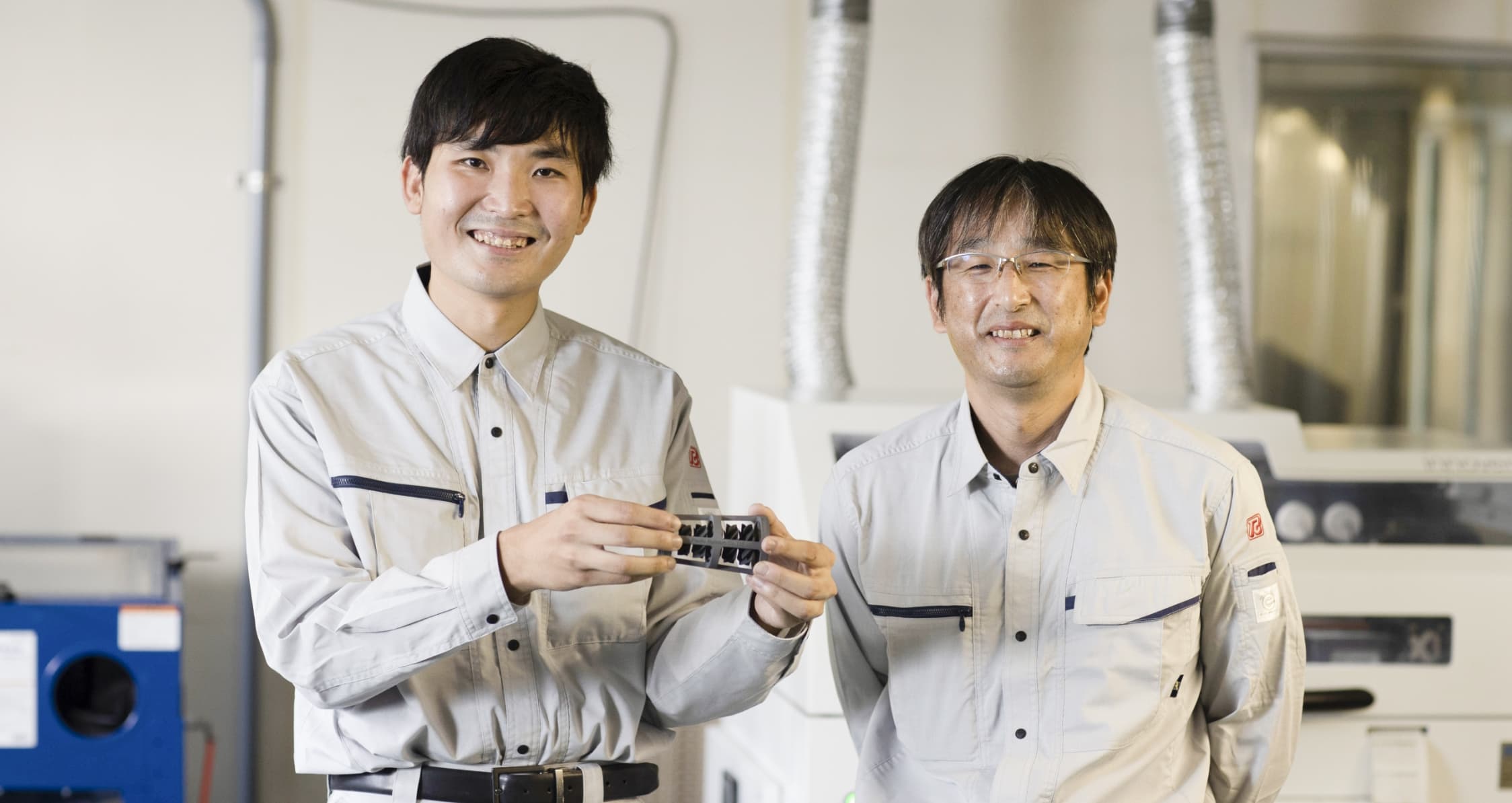